先知輔導案例
各產業輔導案例
太陽能模組廠自動化產業
R2021b 新功能與產品應用
Function | Principle | Benefits for USER |
---|---|---|
登入頁面 | (功能項目)首頁、手動輸入條碼、設定、啟動、停止、重新登入。 | 系統開始頁面,挑選下方EAP選單,選擇需要的機台EAP模組,下方為選擇包護教翻轉機模組畫面(圖一)上方後會新增下方模組、設定PLC IP與Port,當PLC連線時,紅色區塊會轉成綠色的區塊(圖二)。 |
生產資訊設定頁面 | Step1: 常規設定 Step2: LOG設定 Step3: MQTT設定 Step4: 位置規則(掃碼槍)。 |
Step1: 廠區、生產線、設備代碼、工序、是否使用離線範本、選擇離線範本檔案、側標印標機選擇、大標印標機選擇 Step2: LOG保存的時間 、LOG保存路徑 Step3: 是否開啟MQTT資料推送、MQTT Server IP、MQTT代理人Broker)、MQTT推送資料項目選擇(可多選)、Web Service 地址 Step4: 是否有COMPORT掃碼槍、掃碼槍COM選擇、掃碼槍鮑率、掃碼槍資料位元、掃碼槍奇偶校正位元、掃碼槍停止位元。 |
工藝參數收集 | 工藝參數收集與異動確認。 | 工藝參數收集與異動確認。如有異動,將整組工藝參數使用固定的Json格式並透過WebService發送至MES做紀錄保存。 |
Alarm收集 | Alarm參數設定。 | Alarm參數設定: 1.讀取PLC 設定參數異動標誌地址的值。 2.讀取PLC Alarm地址的值。如有異動,則將異動的Alarm使用固定的Json格式並透過WebService發送至MES做紀錄保存。 |
手動輸入條碼 | 手動輸入/重新掃碼。 | 機台復歸後會由人員決定要進行重掃或是手動輸入條碼。 |
粉末燒結自動化與異常監測產業
R2021b 新功能與產品應用
Function | Principle | Benefits for USER |
---|---|---|
多機台監控頁面 | 針對單一製程的機台,提供機台狀態即時監控畫面,包含生產數量與稼動率...等等。 | 現場操作員或設備管理者,可隨時查看監控畫面,即時了解製程中是否有設備發生參數超規異常,生產數量異常或稼動率異常問題。 |
單機台監控頁面 | 從多機台監控畫面可點選任一機台,查看該機台更詳細的即時監控資訊。 | 現場操作員或設備管理者,可隨時查詢異常設備當下的即時詳細加工過程資訊,快速了解異常發生的可能原因,並立刻進行調整與復機。 |
機台設定頁面 | 對每一機台,設定每日稼動率計算起訖時間(有效加工時間)。 | 設備管理者,可針對工廠實際生產情形,設定機台價動率計算時間,以利計算正確數據。 |
異常訊息查詢 | 依據工單,列出工單生產過程的異常明細,並可查詢異常發生當下各監控參數的趨勢圖、上下限設定..等等詳細資訊。 | 設備管理者,可快速取得異常工單生產明細,以及分析異常真因,加速異常報表製作以及制定廠內生產SOP。 |
歷史查詢頁面 | 使用機台、工單、時間起迄..等等進行批量資料查詢,並可依工單一一查看加工過程監控參數趨勢圖、上下限設定...等等加工過程詳細資訊。 | 設備管理者,可快速取得機台或工單生產明細,加速分析每台設備產能,以利進行生產排程。 |
規格設定頁面 | 針對每一個監控參數,設定監控規格上下限值。 | 設備管理者,可依每台設備的情況,制定該設備加工參數卡控規則,避免過多False Alarm 產生。 |
放電加工機自動化與異常監測
R2021b 新功能與產品應用
Function | Principle | Benefits for USER |
---|---|---|
多機台監控頁面 | 針對單一製程的機台,提供機台狀態即時監控畫面,包含生產數量與稼動率...等等。 | 現場操作員或設備管理者,可隨時查看監控畫面,即時了解製程中是否有設備發生參數超規異常,生產數量異常或稼動率異常問題。 |
單機台監控頁面 | 從多機台監控畫面可點選任一機台,查看該機台更詳細的即時監控資訊。 | 現場操作員或設備管理者,可隨時查詢異常設備當下的即時詳細加工過程資訊,快速了解異常發生的可能原因,並立刻進行調整與復機。 |
機台設定頁面 | 對每一機台,設定每日稼動率計算起訖時間(有效加工時間)。 | 設備管理者,可針對工廠實際生產情形,設定機台價動率計算時間,以利計算正確數據。 |
異常訊息查詢 | 依據工單,列出工單生產過程的異常明細,並可查詢異常發生當下各監控參數的趨勢圖、上下限設定..等等詳細資訊。 | 設備管理者,可快速取得異常工單生產明細,以及分析異常真因,加速異常報表製作以及制定廠內生產SOP。 |
歷史查詢頁面 | 使用機台、工單、時間起迄..等等進行批量資料查詢,並可依工單一一查看加工過程監控參數趨勢圖、上下限設定...等等加工過程詳細資訊。 | 設備管理者,可快速取得機台或工單生產明細,加速分析每台設備產能,以利進行生產排程。 |
規格設定頁面 | 針對每一個監控參數,設定監控規格上下限值。 | 設備管理者,可依每台設備的情況,制定該設備加工參數卡控規則,避免過多False Alarm 產生。 |
半導體產業導入建構晶圓測試之針測機Recipe最佳化計畫
輔導案例:〇〇科技股份有限公司(受輔導業者)
計畫成果
建立機台資訊中央系統,串聯機台資訊,統一資訊流向。
中央資訊系統彙總現場測試機台Recipe查核及派發。
建立最佳化Recipe、提高測試良率。
廠內面臨問題
(1) OO科技股份有限公司屬半導體製程的下游,專業為積體電路測試。
(2) 目前IC產業鏈中/上游廠商普遍具備成熟的機聯網及智機化技術,而下游封裝及測試廠多數仍在機聯網之建置或智機化之起步。
(3) 系統級封裝的IC在完成後才能做最終測試,確認發揮整體功能,然而,由設計到最終測試過程中之所需要的測試項目(特性)均不同,因此,測試 Recipe管理的好壞,將決定測試廠決最終的成本及品質。
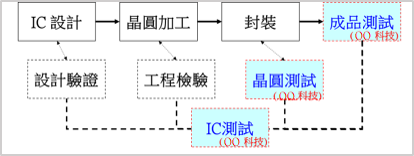
計畫效益
(1)降低品質不良損失金額:因誤植機台探針機參數,導致品質損失15,000,000元/年。
(2)降低設備耗損損失金額:因誤植機台探針機參數,導致機台探針損毀3,000,000元/年。
(3)縮短生產時程:改善50%人員輸入、設定及核對資料時間。
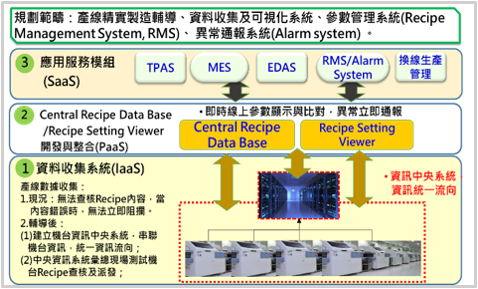
連接器產業導入SMB輔導案例:〇〇工業(受輔導業者)
計畫成果
完成8台自動端子壓著機的機聯網,採用樹莓派Pi4一對二方式進行機台兩種人機資訊解碼三菱與基恩斯。
使用MQTT通訊協定進行資料上報,將資料儲存於後端SMB伺服器進行實際稼動率分析與完工計量計算,易於未來進行資料交換以及於行動平台瀏覽。
SMB伺服器與廠內MES系統進行資訊整合,取得實際工批資訊,進行計畫生產時間與實際生產時間之比較,分析實際生產效能。
廠內面臨問題
(1) 位於新北市汐止區,員工人數約170人
(2) 總端子壓著設備約60台,分散在5個廠區,目前尚未有設備進行機聯網,平常仰賴人工進行巡檢抄表,進行設備生產過程記錄。但通常產品有異常時,無法確認異常當時真正的設備情況,導致分析不易。
(3) 設備效能、稼動率..等等資訊僅能記錄重大停機時間,短時間停機無記錄,導致OEE結果與實際有所落差。
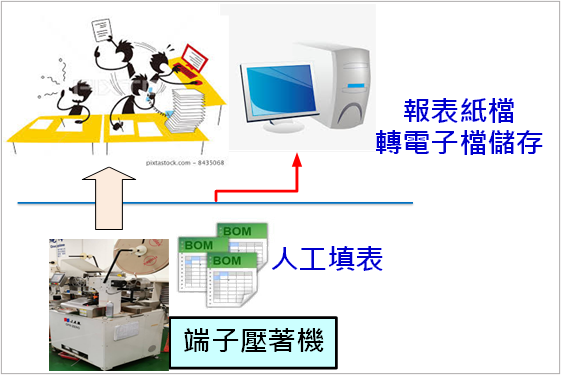
計畫效益
(1)縮短處理生產資訊之時間:機聯網後資訊處理時間由60分鐘縮短至20分鐘,縮短約65%。
(2)降低生產成本 : 機聯網後每台設備每年節省人工成本約40,000元。
(3)提高設備時間可動率(Availability)(%): 設備可動率由68%提升至73%以上。
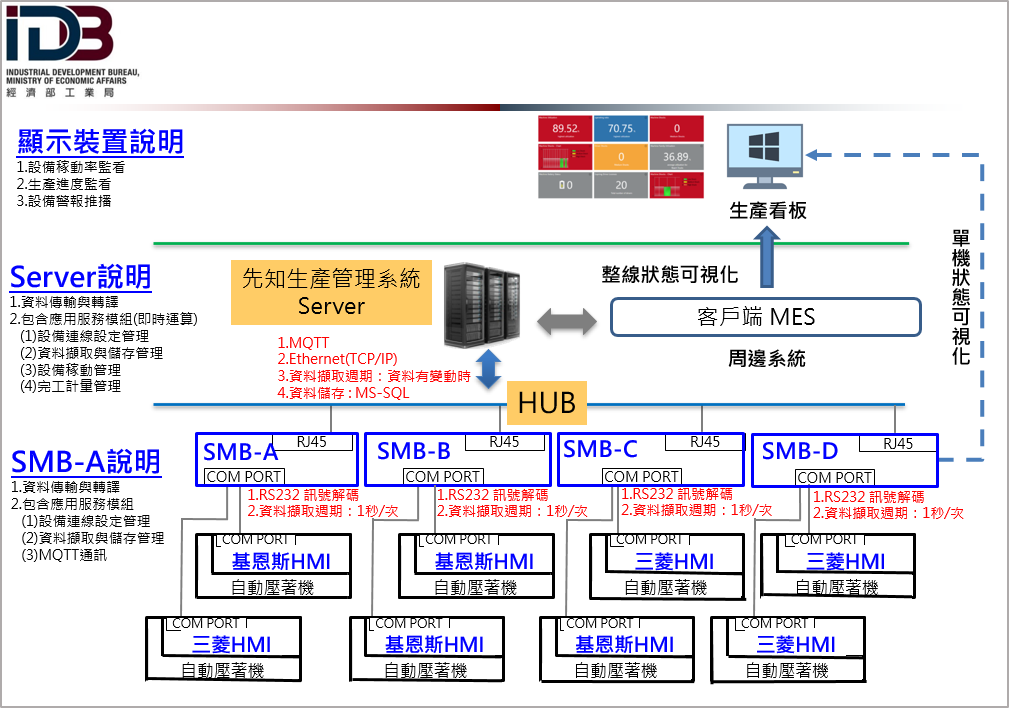
連接器產業導入SMU輔導案例:〇〇工業(受輔導業者)
計畫成果
完成生產管理模組功能擴充,進行現場壓著規格(Recipe)生產前確認,避免報廢品產生。
完成8台自動端子壓著機壓接力感測模組安裝與導入,進行每秒1千筆以上壓接力數值收集與分析,有異常立刻警報於產線看板。
使用MQTT通訊協定進行資料上報,將資料儲存於後端SMB伺服器。
完成刀片保養預警,提前10天預警更換,減少故障停機時間。
廠內面臨問題
(1) 位於新北市汐止區,員工人數約170人
(2) 總端子壓著設備約60 台,分散在5 個廠區,目前製一課 8 台自動壓著機已完成機聯網。可計算實際設備可動率以及完工計量。
(3) 客戶要求產品整體訊號與電源不能因為壓接品質導致產品失效。
(4)歐美中日等國製壓接力監控已經是新生產設備的標準配備,但台灣線束設備廠商在20年前移往中國大陸就已經不再研發,反而是大陸急起直追。

計畫效益
(1)減少退貨處理成本 : 8台設備每年由6萬降至2萬以下。
(2)提高產品良率 : 良率由80%提升至 90%以上。
(3)縮短維護設備導致停機時間 : 每台設備每年48小時無預警停機,減少至15小時以下。
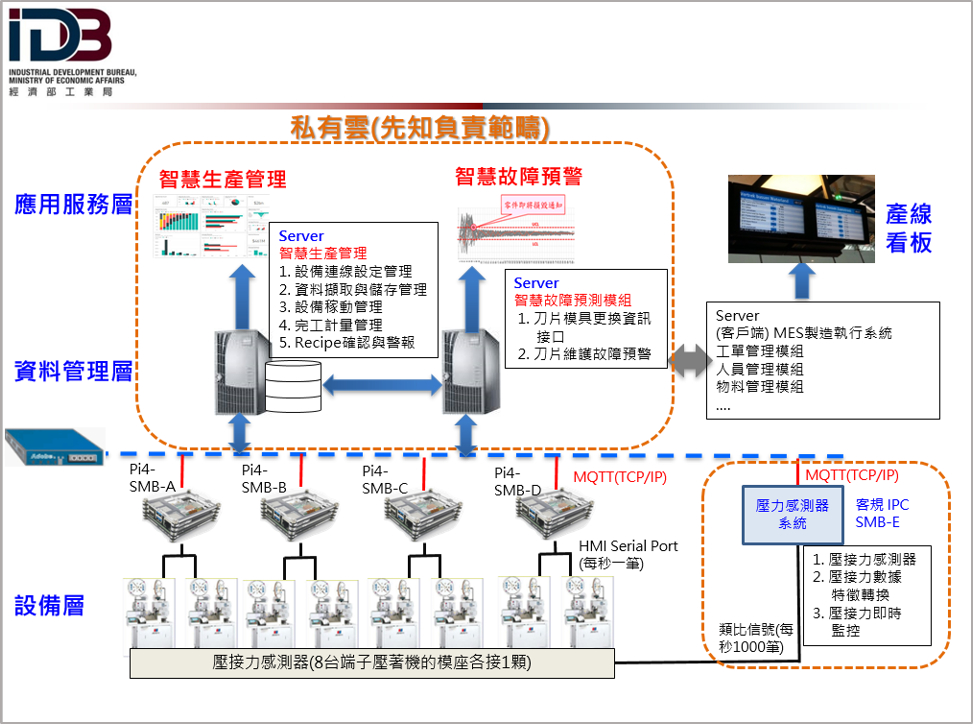
扣件業導入IIOT建置及設備預防保養AI運用:〇〇工業(受輔導業者)
計畫成果:完成扣件業IIOT建置與實現
建立機台感知系統。
建立機聯網及可視化架構。
建立AI監控模組。
整合工廠營運資訊系統。
建立智能化營運機制。
廠內面臨問題
(1) 巡檢員定時、依序進行巡檢,無法即時掌握冷鍛機針頭狀態,機台以每分鐘180隻螺絲的速度生產,當機器針頭異常前若不即時更換,導致每月約產生2,000kgs報廢品。
(2) 設備總合效率OEE低落,無法增加產值。
(3) 物料數據無法掌握,每個月庫存過高,成本約400萬元/月。
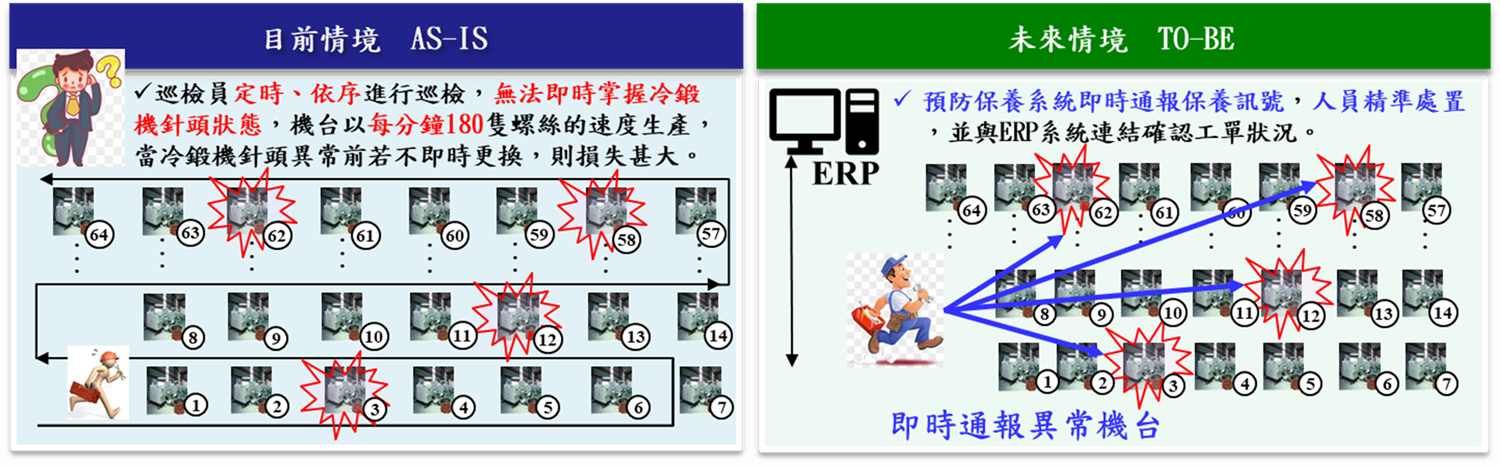
計畫效益
(1)提升產品良率:不良率下降50%,減低損失金額2,400,000元/年。
(2)降低庫存成本:庫存成本下降:5% ,降低庫存成本2,400,000元/年。
(3)提升OEE:導入前72%,導入後75%,提升3%,增加產值16,200,000元/年。
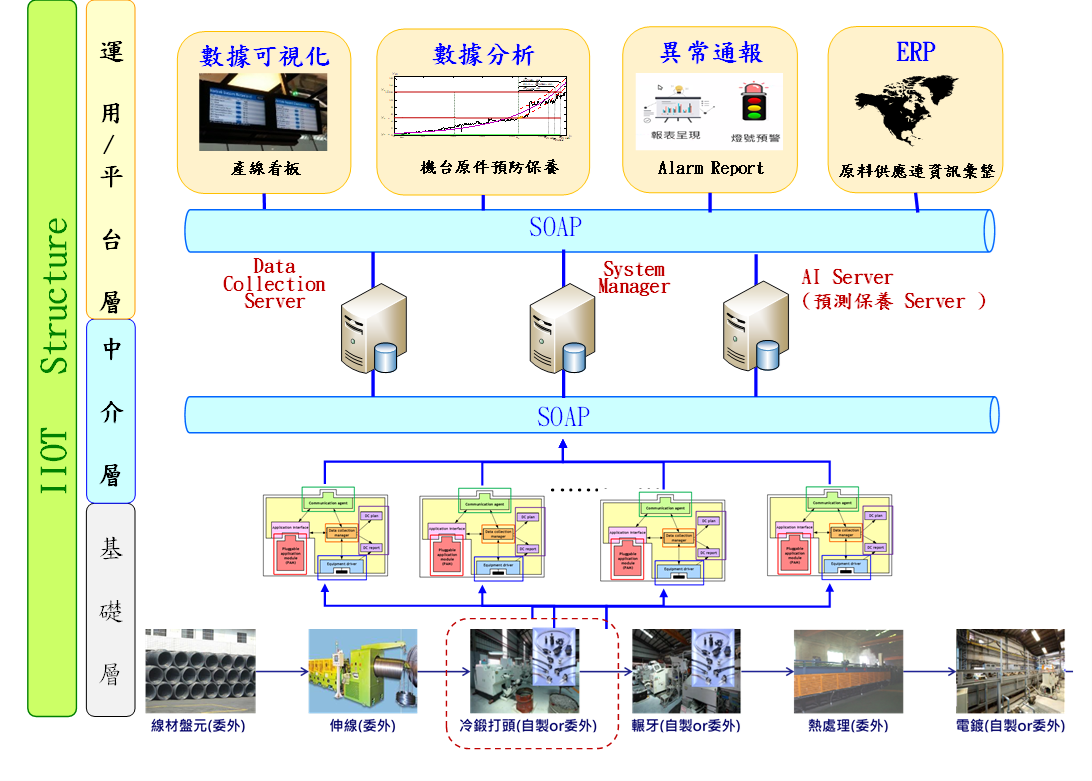
鑽石工具製造產業導入SMU輔導案例:〇〇工業(受輔導業者)
計畫成果:
完成4台燒結爐製程參數異常偵測與分類(FDC)建置,透過每一次燒結的監控得知燒結設備溫度與壓力曲線是否超過標準,增加終端客戶信任度。
完成燒結爐全自動虛擬量測系統(AVM)建置,將燒結製程提升至接近工業4.0的智慧工廠境界,因AVM具有線上即時全檢與肇因分析的能力,可達到製造零缺陷的目標,提升公司形象。
廠內面臨問題
(1) 製造風險:
製程皆為單機生產,產線上的資訊缺乏即時數位化,導致人事成本增加、報廢、耗時等問題,製程參數即時控管的影響最為嚴重,其因工件成本高、燒結製程時間長約一小時,倘若在生產時無法即時察覺燒結爐溫度、壓力的異常狀況,並馬上進行調整,其成品在客戶的回饋上使用壽命都較正常的縮短20~25%的時間,這部分的客訴會影響後續的訂單,相對得會使公司年度獲利降低。
(2) 品質風險:
目前燒結半成品皆為人工用游標卡尺進行內外徑、最高和最低點的量測,一顆燒結半成品的檢測大約15~25分鐘不等(含人工寫入量測資料資料時間)。換算下來一個員工8小時只能量測約30顆半成品(抽測率約10%)。由於客戶對品質的要求逐漸提升,目前抽測的方式難以保證到客戶端的產品都是好的。如何全面控管生產品質,確保出貨品質零缺陷,也是廠內所面臨需要解決的困難。
計畫效益
(1)整合生產與量測資料,加速資料的可追朔性,生產與量測資料核對與查詢時間由20分鐘→5分鐘內。
(2)縮短排除設備故障之時間: 降低作業員進行製程異常資料收集和異常資料分析與報告製作時間,由原本120分鐘→30分鐘。
(3)提供每顆產品的燒結量測結果: 全面提供虛擬量測結果由抽測率 10% →提升 100% 。
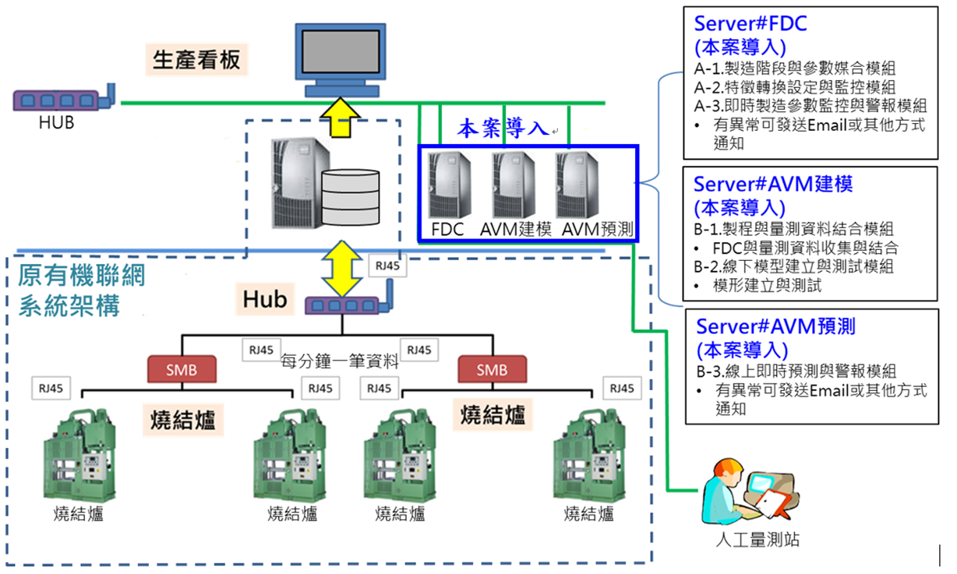